FikusPlus 22 5-axis milling: a competitive advantage
Discover the benefits of 5-axis milling with FikusPlus
The new version of FikusPlus 22 incorporates 5-axis positioned milling, giving FikusPlus users a competitive advantage over traditional 3-axis machining systems.
The term "5-axis" refers to the number of directions in which the cutting tool can move. 5-axis machining involves moving the cutting tool and workpiece using the X, Y and Z linear axes and rotating two of the three axes A, B or C simultaneously during a machining operation. Programmers can take advantage of the three linear axes and, in addition, add 2 of the 3 possible rotary axes: A (rotation around the X axis), B (rotation around the Y axis) and/or C (rotation around the Z axis).
5-axis machining allows you to work on the part from any direction, processing all five sides of a part in a single setup. As a result, where 5-axis CNC machining excels is in its ability to create complex shapes within a single setup.
Types of 5-axis machining
There are two types of 5-axis machining: positioned and continuous. In positioned 5-axis machining, also called 3+2, which is implemented by FikusPlus 22, the A and B or C axes remain fixed (positioned) and only move when changing from one orientation to another. In continuous 5-axis machining, all 5 axes move simultaneously.
Automatic Feature Recognition on 5 positioned axes
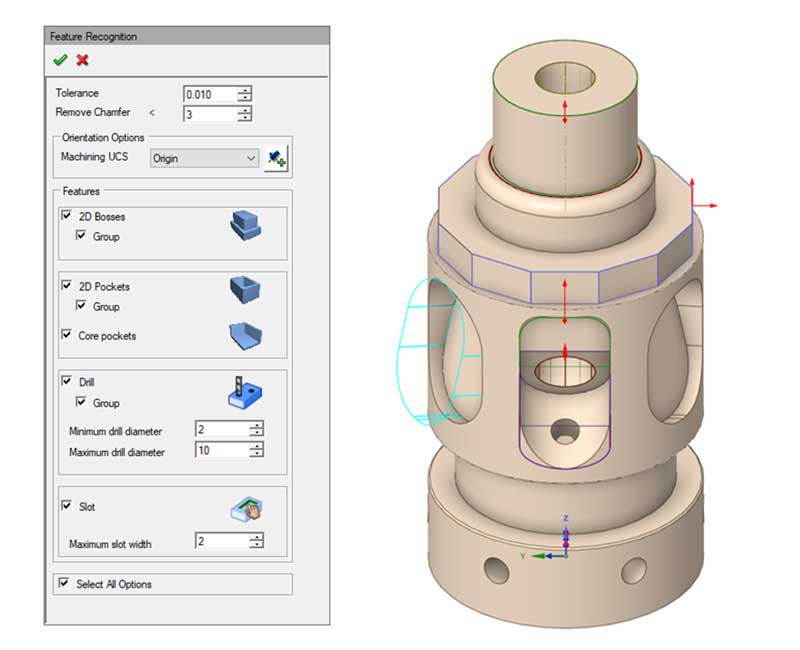
The 4 advantages of 5-axis machining
- Shorter lead time. By machining the part in a single set-up, we eliminate downtime due to the preparation of the different set-ups.
- Higher quality by using shorter cutting tools drastically reducing vibration and pressure on the cutter, providing a better surface finish.
- Increased manufacturing precision of the parts, eliminating possible imperfections when machining in different setups.
- Reduced risk of errors by reducing all human intervention to a single part positioning.
5-axis CNC milling machine
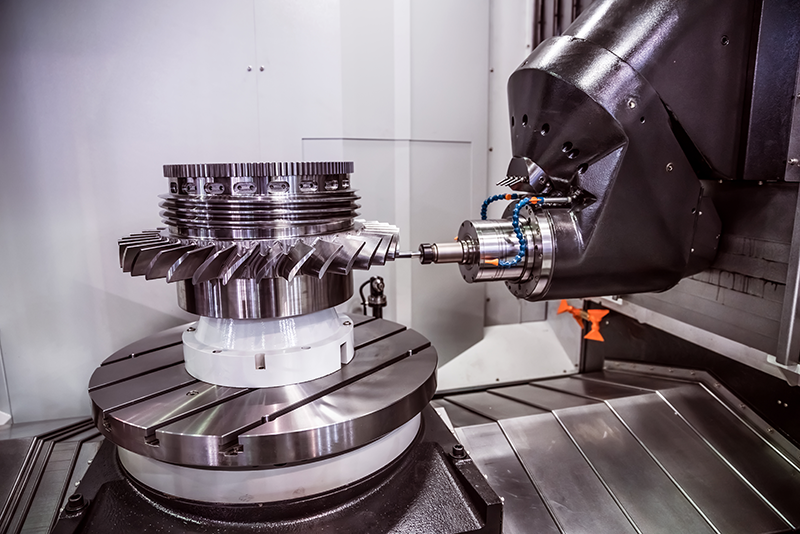